We have a traditional commitment to quality. We strive to
achieve excellence in our products, service and delivery. Throughout the
years, we have won the confidence of popular brand names such as Gymboree,
Gap, Pottery Barn and Next.
Process |
Description |
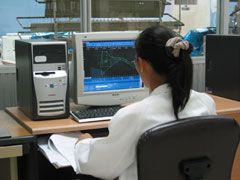 |
The first step to produce high quality garments
is to have correct patterns. At Asia Thai Product, we use "Gerber
Accumark System" to streamline our pattern, grading and marker
making processes. |
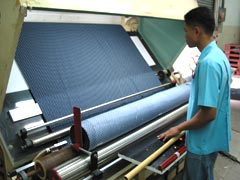 |
Fabric shading and defect are major problems for garment
production. At Asia Thai Product, we carefully check every yard of
fabric with cloth inspection machine. |
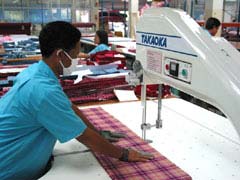
|
Our cutting staff is operating a bandknife machine. |
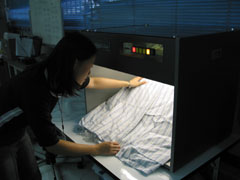 |
Our quality control staff employs light box to check
fabric shading. |
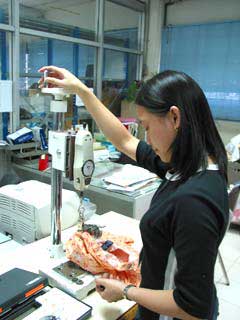 |
Since majority of our products are for babies and
kids, we put extra care in testing strength of snaps, buttons and
other accessories on garments. Routinely, we sample garments from
production line to do the pull strength test to ensure that our
products meet pull strength requirements.
- Quality control staff uses "SafQ Strength Testing Equipment"
to determine the physical safety and reliability of snaps, buttons
and other accessories on garments. |
|
With the implementation of bar-code tracking production
system, we are able to know in real time the progression of our production
processes. This enables us to speed up production and solve bottleneck
problems. Thus, we can gaurantee on time product delivery to our customers. |
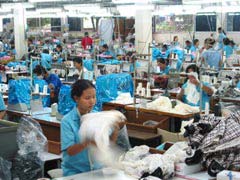 |
Productivity is our key competitive advantage. Our
workers are equipped with modern industrial sewing machines such brands
as JUKI, BROTHER, PEGASUS, etc. |
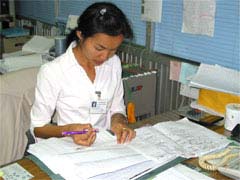
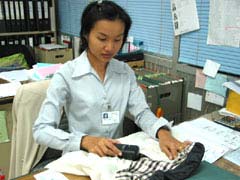
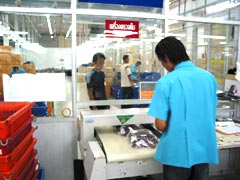 |
Needle control procedures are implemented stringently
in our factory. When the sewing operator breaks a needle, every
effort is made to locate all of the needle fragments. The sewing
operator has to report to authorized plant personnel with all needle
fragments to get replacement needle. If all needle fragments cannot
be found, the components or garments being sewn, including surrounding
components/garments, will be taken to a separate area for thorough
examination. If all the needle fragments still cannot be found,
the component or garment being sewn will be destroyed.
- Needle breakage control staff is recording needle breakage incidents
in the Broken Needle Log. (top picture)
- Needle breakage control staff is using 'Nissin' needle detector
device to search for needle fragments on garment. (middle picture)
- All finished garments must pass needle detector machine before
they are passed to packing room. (bottom picture) |
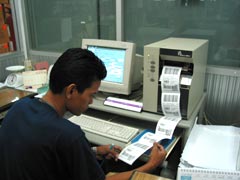 |
With the implementation of Electronic Data Interchange
(EDI) package called "REDI-to-Wear™", we are able
to increase the efficiency and timeliness of communication with
our customers.
- Using "REDI-to-Wear™" program, our staff is printing
bar-code labels to place on cartons before ex-factory. |